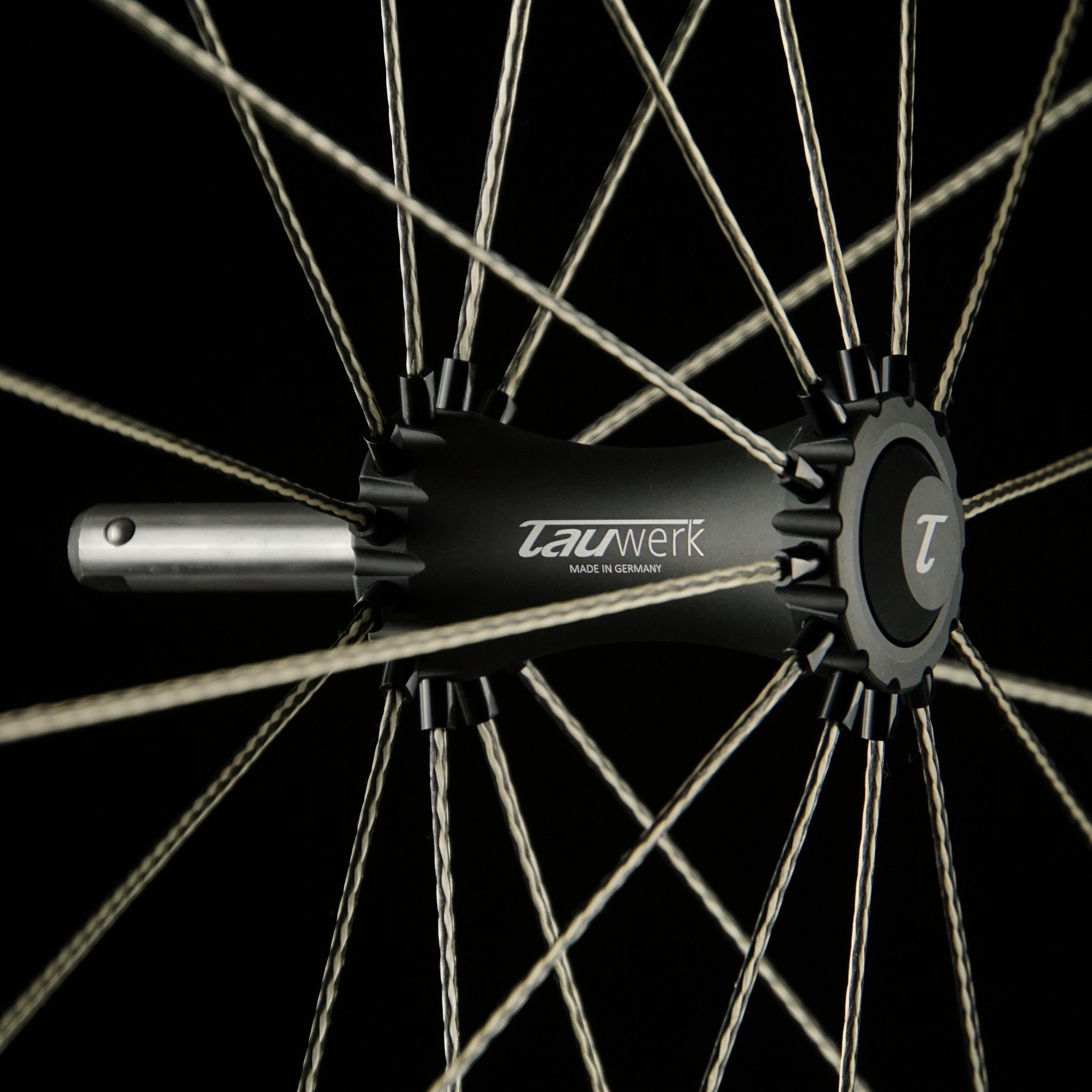
Technology
Our wheels are no ordinary wheels, they push the boundaries of what is possible.
The aim of the development was to produce the lightest wheelchair wheel in the world - without compromise.
Every component has been revised and conventional technologies were rethought.
Engineering
It is not trivial to create exceptional products. Even if mechanical engineering occasionally has a somewhat dry, less emotional image, we use our knowledge in theory of material strength, materials engineering, design theory and machine elements to create our extraordinary products. This does not mean that all effort can only lead to one result. Every outstanding product carries not only the signature and ideas of the developers, but also those of the users. That's why it's called engineering: the art of knowing what a product needs to become indispensable. And that is why there is no standstill in development.
Patented textile spokes
The main feature of all Tauwerk wheels are the patented spokes made of high-strength synthetic fibers. Our spokes, unique in the wheelchair market, are manufactured in Chemnitz (Germany), individually tested and carefully assembled.
In addition to ultra-light weight and maximum durability, they are also unique in design due to their braided structure.
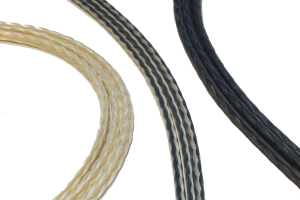
further specifications
The fiber we use has good abrasion resistance and absorbs virtually no moisture. A special coating protects the fibers from UV light. The coating also significantly reduces the susceptibility to dirt. The fiber has high stiffness with practically negligible creep. Therefore ideal for spokes in a wheel, which are subjected exclusively to tensile forces.
The fiber yarn is braided into ropes in our house, which gives us the opportunity to produce patterns from differently colored yarns, creating a unique look. The feel of interlaced and tensioned ropes is also impressive and certainly unique. The ropes are then further "heat-set" under high load and temperature, which further improves their properties in terms of elongation and surface quality.
In further work steps, the ropes are hand-fitted with non-detachable end connections made of high-strength aluminum and completed to form the finished spoke. The end connections allow a precise centering of the rim by means of fine threads. The static tensile strength of our spokes is more than 2000 Newtons, which corresponds to a weight force of more than 200 kg. The tensile strength of the rope itself is even more than 7000 Newtons. Since ropes per se cannot absorb bending moments, they evade lateral loads and return to their original shape after loading. The increased tensile stresses in the spoke that occur briefly in the process do not pose a problem. Damage or permanent deformation of the spokes caused by dull objects, as can occur with steel spokes - for example when loading the wheels in a vehicle - is thus ruled out.
Our textile spokes weigh 65% less than conventional steel spokes and are at least 20% lighter than our competitors lightest spokes to date.
min.
0
N
Tensile strength
min.
0
%
Driving pleasure
min.
0
% lighter
than other wheelchair spokes
*than conventional steel spokes
Ultra light carbon rims
After some searching for rim manufacturers that meet our requirements in terms of know-how and manufacturing quality, we found the perfect partner or the development of outstanding carbon rims: the Austrian Company Xentis®. The result of the development are rims that are probably unparalleled in the wheelchair sector when it comes to design, reliability and low weight.
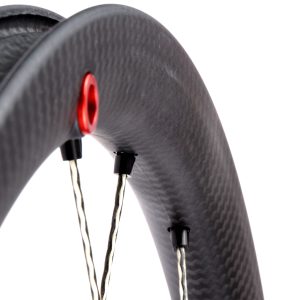
further specifications
The 28 mm high rim has an outer width of 25.4 mm. This harmonizes visually and technically perfectly with the widely used 1" (25.4 mm) wide tires - for example, the Schwalbe® One; Marathon or Rightrun.
The 17 mm inner width of the rim, however, also allow all other common tire widths between 20 mm and 37 mm. Two minimal humps in the rim bed ensure the precise fit and concentricity of the tires, even at low air pressures.
The rims are manufactured in a predominantly manual process to 100 % in Austria. The areas of the spoke seats are extra reinforced and thus grant a permanently stable connection to the spokes.
Despite the very low rim weight of only 340 g with a diameter of 540 mm (24"), the rim has optimum rigidity and strength for everyday use. Each rim has a serial number and RFID chip, which ensures the traceability of origin and production
The valve bore has a diameter of 9 mm due to production and is reduced via an insert to 6.5 mm for the use of hoses with Sclaverand valve. The use of tubes with Schrader valve (car valve) is possible, but we advise for technical and optical reasons to the more pressure-stable Sclaverand valves. For a 1" wide tire, the rims are approved up to a pressure of 10 bar.
0
g
Rim weight
0
bar
Maximum pressure
0
%
made in Austria
at 24″ x 1″
High strength aluminum hubs
We manufacture our hubs from an innovative aluminum alloy whose development goes back to aerospace technology. Compared to steel, it has a 66 % lower density with sufficiently high strength. In addition, it can be used to manufacture modern hub designs.
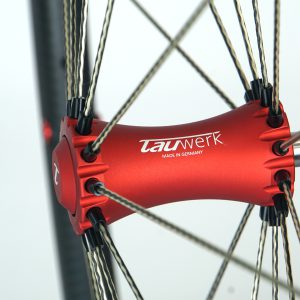
further specifications
The design of the hubs is geared to optimally absorbing and dissipating the external loads acting on them. “The aim was to achieve an uniformly high load on the entire material and thus avoid areas with excessively high stresses. Modern design and simulation tools provided valuable support here.
Our paver's revolutionary surface blasting technology enables us to produce defined, absolutely uniform and 100% reproducible surfaces.
Any machining marks are thus completely removed, giving the hubs a superior look and feel. In addition, shot blasting further increases the strength of the areas near the surface.
<
0
g
Hub weight
0
%
Lighter than steel
0
%
even surface
Low friction ceramic bearings
We use high-quality ceramic bearings in our Tauwerk wheels. Ceramic bearings with their very hard and extraordinarily wear-resistant rolling elements made of silicon nitride impress with significantly lower friction and an unsurpassed service life compared to standard ball bearings with steel balls.
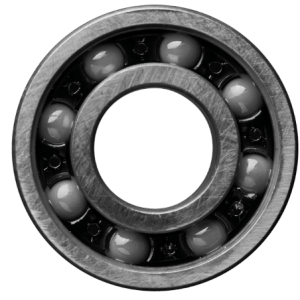
further specifications
Ceramic bearings, for example the ceramicspeed® bearings handmade in Denmark, have shown to run quieter and lighter. They offer 5 to 10 times the service life of standard bearings - even under heavy loads. We think there is no reason to install other bearings in Tauwerk delight.
Our wheels are available for axle diameter 12 mm and 12.7 mm (1/2 inch). The bearing distance is 56 mm (outside/outside).
Six point push rims
The push rims are bolted axially to the rim at six points. This type of fastening gives us a more organic and overall much more attractive design than the usual protruding and bent push rim lugs. But this variant also offers advantages over the attachment method with lugs in terms of strength, assembly effort, push rim positioning and risk of injury.
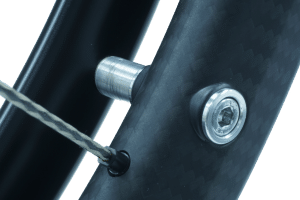
further specifications
The push rim distance to the rim is optically cleanly adjusted via spacer sleeves and can also be easily set to individual requirements at any time, even with the tire fitted. All wheels are supplied with corresponding spacers made of anodized aluminum. The bolt-on points on the rim consist of positive-locking, captive inserts made of the same aluminum and permanently ensure a stable flow of force between the handrim and the wheel. We only use titanium screws for the best combination of high strength and low weight.
We only use high-quality and lightweight hand rims from Carbolife®. These are also "made in germany" and, thanks to their innovative ergonomic profile shape, ensure a force-saving, controlled and fatigue-free grip. The hand rims are available in different variants.
Final assembly by hand
Each Tauwerk wheel is carefully spoked, centered and pressed several times by hand at our Chemnitz facility. For each wheel, the spoke tensions of all spokes as well as the radial and axial runout of the rim are electronically recorded and documented. The repeated defined pressing permanently avoids a renewed (re)centering of the Tauwerk wheels during proper use.
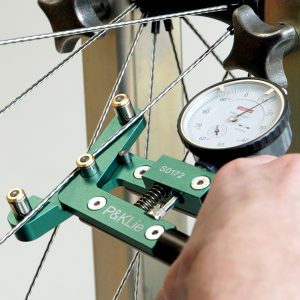
further specifications
Tauwerk wheels are radially spoked, i.e. the spokes do not cross and run along the shortest possible path from the hub to the rim. This achieves maximum wheel stiffness in the transverse direction while minimizing overall weight. Crossed lacing, as is usually found on bicycle wheels, is not necessary on wheelchair wheels because no torque needs to be transmitted in the direction of travel between the hub and the rim. In contrast to the bicycle sector, the drive and braking forces on the wheelchair are introduced directly into the rim via the push rim and do not first act on the hub. Contrary to widespread opinion, crossed lacing also does not result in increased stiffness or stability in the case of loads acting in the wheelchair area.
The oval spokes are aligned in the direction of travel, resulting in a uniform and dynamic appearance, similar to the so-called "knife spokes" in the bicycle sector.
We center all wheels with a lateral and radial runout tolerance of +/- 0.2 mm and a high spoke tension that is as uniform as possible per side. This ensures that the wheel can permanently bear the loads acting during operation without individual spokes being able to briefly lose their tensile stress - and thus become loose - or overloaded.
The wheels are pressed by hand several times during this process. This eliminates further settling of the spokes during usage and the associated out-of-round running.
Do you want to pre-order a cordage wheel today?
Contact us via contact@bravecomponents.com and we will send you more information.